Low US Household Leverage Bodes Well For The Economy
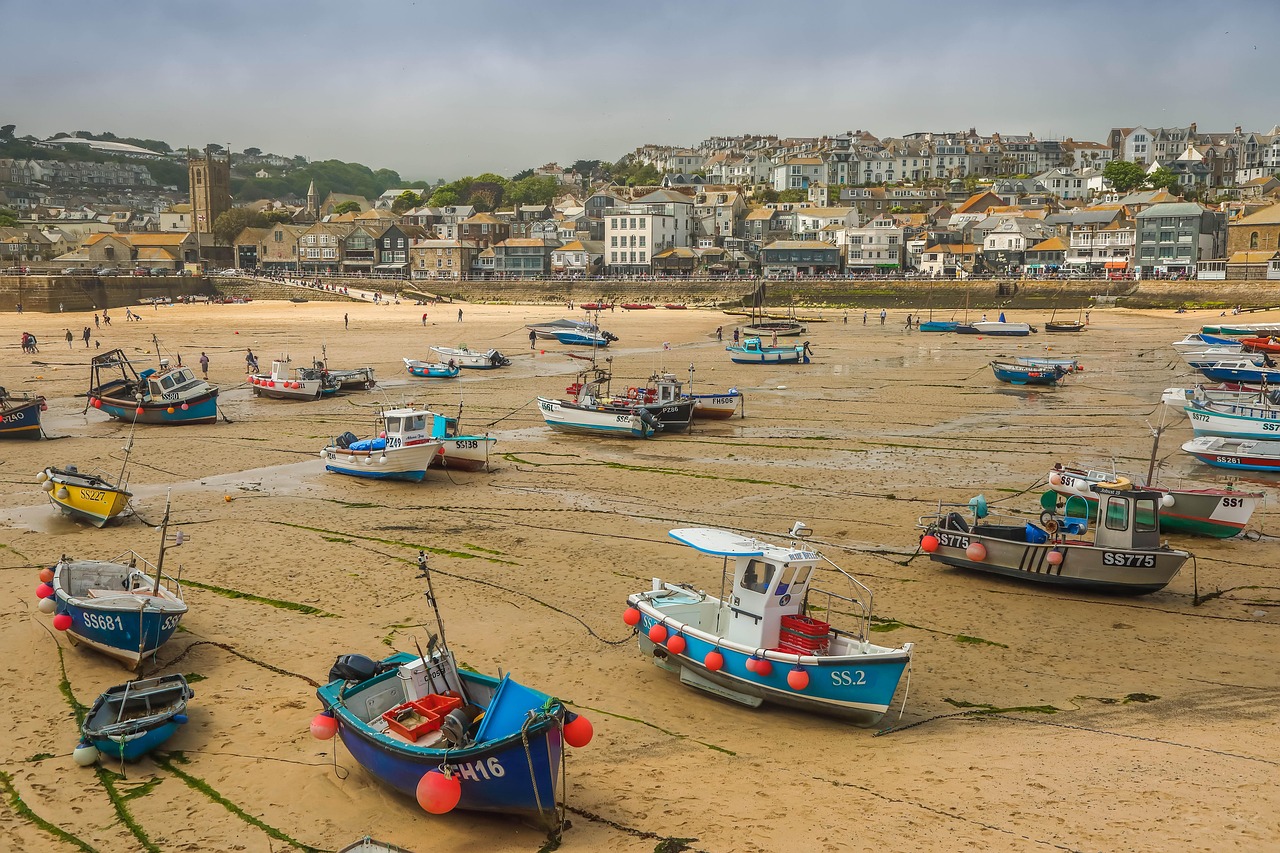
One of the things that gives me great comfort about the health of the U.S. economy is our historically low household leverage. According to the Federal Reserve Board, household leverage is now at an 80-year low—a remarkable sign of financial discipline.
So let me be the first to congratulate you for not loading up on debt like so many did between 2000 and 2008, right before the worst financial crisis of our lifetimes!
Back then, people lost their jobs and massive chunks of their net worth because of too much leverage. I was one of them—I had two mortgages and ended up losing 35% to 40% of my net worth in just six months. It took a decade to rebuild.
After that experience, I promised myself: never again will I take on that much debt.

Households Can Better Withstand the Next Recession
Nobody likes a recession or stagflation. But with household leverage at an 80-year low, it’s highly unlikely we’ll face another global financial crisis like in 2009. Households are simply too cashed up to panic-sell. Instead, most will hunker down and wait for better times to return.
Thanks to this strength, I plan to use any correction as an opportunity to buy the dip—for both my retirement accounts and my children’s. With so much cash on the sidelines, we’re more likely to see V-shaped recoveries than drawn-out U-shaped ones.
Personally, after selling our previous rental, I’m sitting on ample liquidity in Treasury bills and public stocks I can sell and settle within days. And with a fully paid-off primary residence, there’s almost zero chance I’ll ever sell at a discount. Why would I, with no mortgage and no urgency? Around 40% of U.S. homeowners now own their properties outright.
Just imagine how much the stock market, real estate, and Bitcoin could surge if household leverage ever returns to 2007 levels. Risk assets would likely skyrocket once again. And based on human nature and our historical appetite for risk, I wouldn’t be surprised if leverage ramps back up, especially as interest rates continue to decline.

On top of that, millions of homeowners locked in rock-bottom mortgage rates in 2020 and 2021. The tappable home equity across the country is enormous compared to 2007, making another housing-driven crash highly unlikely.

The Only Good Type of Leverage
In general, the less debt you have, the better. But in a bull market, strategic leverage can accelerate wealth building. So what’s a financial freedom seeker supposed to do?
First, understand that not all debt is created equal. Consumer debt, especially from credit cards, is the worst kind of widely available debt. With average credit card interest rates north of 25%, you’re basically giving your lender a return Warren Buffett himself would envy. For the love of all that’s good in this world, avoid revolving consumer debt at all costs.
The only type of debt I condone is mortgage debt used to build long-term wealth. It’s generally one of the lowest-cost forms of borrowing because it’s secured by a real, usable asset. Being able to leverage up 5:1 by putting just 20% down to buy a home—and then live in it for free or even profit—is an incredible opportunity.
That’s why I’m a strong proponent of everyone at least getting neutral real estate by owning their primary residence. Hold it long enough, and thanks to forced savings, inflation, and mostly fixed housing costs, you’ll likely come out far ahead compared to renting a similar place. People like to say they will save and invest the difference, but most people can’t keep it up over the long term.
As for margin debt to invest in stocks? I’m not a fan. Stocks offer no utility, are more volatile, and margin rates are usually much higher than mortgage rates. If you’re going to use debt, at least tie it to something you can live in and control.

The Recommended Asset-To-Debt Ratio By Age
Here’s a useful framework to assess your financial health: a suggested asset-to-debt (liability) ratio, paired with a target net worth by age. The asset-to-debt ratio applies broadly, regardless of income.
The net worth targets assume a household earning between $150,000 to $300,000 during their working years, maxing out their 401(k), saving an additional 20% of after-401(k) income, and owning a primary residence. In short, aim for a net worth equal to 20X your average household income if you want to feel financially free.

After running the numbers and reflecting on real-world conditions, I believe most people should aim for a steady-state asset-to-liability ratio of at least 5:1 during their highest earning years to retire comfortably.
Why 5:1? Because having five times more assets than liabilities puts you in a strong position to ride out economic storms. Ideally, your debt is tied to appreciating assets—like real estate—not high-interest consumer debt. If your liabilities equal about 20% of your assets, you’re still benefiting from some leverage, without taking excessive risk.
By your 60s and beyond, the goal should shift toward being completely debt-free. An asset-to-liability ratio of 10:1 or higher is ideal at this stage—for example, $1 million in assets and $100,000 in remaining mortgage debt. At this point, most people are eager to eliminate all debt for peace of mind and maximum financial flexibility in retirement.
The peace of mind and flexibility that come with zero debt (infinity ratio) in retirement is hard to overstate.
Be OK With No Longer Maximizing Every Dollar
After selling my former primary residence—which I rented out for a year—I wiped out about $1.4 million in mortgage debt. Even though the rate was low, it feels great to have one less property to manage. Now, with just one mortgage remaining as I approach 50, life feels simpler and a little more manageable.
When my 2.625% ARM resets to 4.625% in the second half of 2026, I may begin paying down extra principal monthly. By then, I expect the 10-year bond yield to be lower, making paying down debt more appealing. While I might miss out on further upside if San Francisco real estate keeps climbing—especially with the AI boom—I no longer care about squeezing out every dollar with leverage.
I’ve built a large enough financial foundation to feel secure. These days, I’m optimizing for simplicity, steady income, and gradual appreciation—the kind that helps me sleep well at night. Chances are, once you hit your 50s, you’ll feel the same too.
The drive to maximize returns eventually takes a backseat to the desire for clarity, peace, and freedom with the time we have left.
Readers, what’s your current asset-to-debt ratio? Are you surprised U.S. household leverage is at an 80-year low? Do you think another recession as long and deep as 2009 is likely? And do you hope to be completely debt-free by the time you retire?
Optimize Your Leverage With A Free Financial Check-Up
One of the biggest signs of a healthy economy today is the fact that U.S. household leverage is near an 80-year low. If you’re working toward becoming debt-free and want to ensure your net worth is positioned for both growth and stability, consider getting a free financial analysis from Empower.
If you have over $100,000 in investable assets—whether in a taxable brokerage account, 401(k), IRA, or savings—a seasoned Empower financial advisor can help you assess your portfolio with fresh eyes. This no-obligation session could uncover inefficient allocations, unnecessary fees, and opportunities to better align your financial structure with your long-term goals.
A sound asset-to-debt ratio and clear investment strategy are key to lasting financial independence. Empower can help you stress test both.
Get your free check-up here and take one step closer to optimizing your financial foundation.
(Disclosure: This statement is provided to you by Financial Samurai (“Promoter”), who has entered into a written referral agreement with Empower Advisory Group, LLC (“EAG”). Learn more here.)
Diversify Your Assets While Reducing Risk Exposure
As you reduce debt, it’s smart to also diversify your investments. In addition to stocks and bonds, private real estate offers an appealing combination of income generation and capital appreciation. With an investment minimum of only $10, you don’t need to take out a mortgage to invest either.
That’s why I’ve invested over $400,000 with Fundrise, a private real estate platform that lets you invest 100% passively in residential and industrial properties across the Sunbelt, where valuations are more reasonable and yield potential is higher.
Fundrise also offers venture exposure to top-tier private AI companies like OpenAI, Anthropic, Databricks, and Anduril through Fundrise Venture. If you believe in the long-term potential of AI but can’t directly invest in these names, this is a unique way to get access.

Fundrise is a long-time sponsor of Financial Samurai as our investment philosophies are aligned. I invest in what I believe in. I have a goal of building a $500,000 position with regular dollar-cost averaging each year.
Subscribe To Financial Samurai
Listen and subscribe to The Financial Samurai podcast on Apple or Spotify. I interview experts in their respective fields and discuss some of the most interesting topics on this site. Your shares, ratings, and reviews are appreciated.
To expedite your journey to financial freedom, join over 60,000 others and subscribe to the free Financial Samurai newsletter. Financial Samurai is among the largest independently-owned personal finance websites, established in 2009. Everything is written based on firsthand experience and expertise.
Source: Low US Household Leverage Bodes Well For The Economy